Vertical pumps are widely used in various industries, including oil and gas, power generation, water treatment, and chemical processing. These pumps play a crucial role in transferring fluids from a lower to a higher elevation, making them essential for many industrial processes. To ensure optimal performance and longevity, vertical pumps rely on a component known as the thrust bearing. In this article, we will explore the importance of vertical pump thrust bearings, their function, types, and the key considerations for their selection and maintenance.
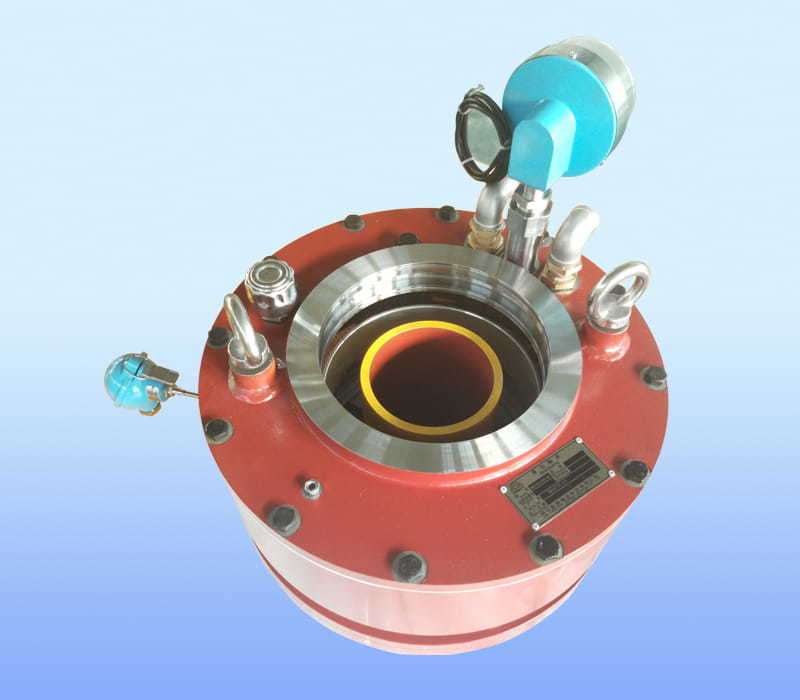
Vertical pumps generate a significant amount of thrust due to the pressure difference between the suction and discharge sides. This thrust force is exerted axially along the pump shaft. Thrust bearings are designed to support and manage this axial load, minimizing the wear and tear on the pump's internal components and ensuring smooth operation. By reducing friction and preventing excessive axial movement, thrust bearings enhance pump efficiency, reliability, and service life.
Types of Vertical Pump Thrust Bearings:
Ball Bearings: Ball bearings are the most common type of thrust bearings used in vertical pumps. They consist of a set of precision steel balls arranged in a cage. These bearings offer low friction and high load-carrying capacity, making them suitable for most vertical pump applications.
Roller Bearings: Roller thrust bearings utilize cylindrical or tapered rollers to support axial loads. They have a larger contact area compared to ball bearings, enabling them to handle higher loads. Roller bearings are commonly used in heavy-duty vertical pumps that operate under extreme conditions.
Fluid-Film Bearings: Fluid-film bearings, such as tilting pad and fixed pad bearings, rely on a thin film of lubricating fluid to separate the rotating shaft from the stationary bearing surface. These bearings offer excellent load-carrying capacity, vibration damping, and self-alignment capabilities. Fluid-film bearings are often employed in large vertical pumps operating at high speeds.
Considerations for Thrust Bearing Selection:
Selecting the appropriate thrust bearing for a vertical pump requires careful consideration of various factors, including:
Load Capacity: The thrust bearing should have sufficient load capacity to handle the axial forces generated by the pump. The operating conditions, such as flow rate, pressure, and impeller size, should be taken into account when determining the load requirements.
Lubrication: Proper lubrication is vital for the smooth operation of thrust bearings. Depending on the bearing type, lubrication can be achieved through oil baths, grease, or oil mist systems. Adequate lubrication minimizes friction, heat generation, and wear, ensuring optimal performance and longevity.
Misalignment Compensation: Vertical pumps are susceptible to misalignment due to various factors, including thermal expansion and shaft deflection. Thrust bearings with self-alignment features, such as tilting pads or self-aligning roller bearings, can compensate for these misalignments, reducing the risk of premature failure.
Maintenance and Monitoring:
Regular maintenance and monitoring are essential to ensure the continued performance of vertical pump thrust bearings. Some key practices include:
Lubrication: Regularly check and replenish lubricants according to the manufacturer's recommendations. Monitor oil quality, temperature, and flow rates to ensure effective lubrication.
Vibration Analysis: Implement vibration analysis techniques to detect any abnormalities in the thrust bearing. Unusual vibrations can indicate misalignment, imbalance, or bearing wear, allowing for timely corrective action.
Temperature Monitoring: Keep a close eye on bearing temperatures, as excessive heat can lead to premature bearing failure. Utilize temperature monitoring devices to identify potential issues and take corrective measures promptly.